I came across a Kickstarter a couple of years ago that offered a CNC machine (Maslow CNC) that could cut 4’x8′ sheets of plywood for under $500. (For those who don’t know: A CNC machine allows the user to draw what they want to cut or carve, convert that drawing into x and y coordinates, and then have a router cut or carve that drawing into a flat material, usually wood, foam or plexiglass. A large CNC machine for home users can usually cut a surface area around 30″ x 30″ and costs somewhere between $1500 to $2500. A cabinet shop might buy a 4′ x 8′ CNC machine for $15,000) This seemed like a steal, so I backed it and received my kit in the mail. Obviously, that price point meant that this wasn’t a plug and play purchase, so it sat on a shelf for years waiting for me to get to it. But I finally built it with this project in mind.

I started my quest to join the FOM shortly thereafter, which included designing a portable bar for the FOM. I naively thought someone was going to build that bar and wanted to make it right, so I actually built the bar to make sure all the dimensions were correct.

I included plans to build flat pack stools based on the FOM logo, and built a prototype with basic tools.

But the real concept looked more like this

I knew I had this CNC machine sitting on the shelf and always planned to get back to it, so I finally decided to put it together so I could build a set of stools for the portable bar, and donate one to the Ohana auction this year.
I already had the basic plans from the portable bar design and bookshelf designs I made previously…

I could have used all of that information to:
- draw it all with a 2D CAD program,
- convert the CAD file into a specialized graphic file,
- import that file into a different conversion program,
- create all the tool paths for the router to cut,
- then convert that file into the language that the CNC machine uses,
- and finally cut the parts out of the plywood.
I already figured out how to do everything in that list, but I am a sucker for punishment. There is a program called Fusion 360 that allows the user to do all of the tasks described above in one program… and 3D model the parts to make sure they fit together correctly, and make universal tweaks that will be applied to all the parts simultaneously.






I decided to give Fusion 360 a try, and my nightmare began…
I watched over 5 hours of online instructional videos (manufacturers’ videos, YouTube, Lynda, etc..) and got to work. “Work” turned into me screaming “THIS PROGRAM IS INCOMPREHENSIBLE! NOTHING MAKES SENSE! WHY CAN’T I DO THAT! WHY IS THIS SO HARD!” as I banged my fists against my desk.
I finally gave up and hired an artist from Calgary to tutor me. We were able to draw the stools over four hours of tutor sessions, but he only knew the drawing part of the program. I tried to figure out the rest and somehow cut the stools in half.
I couldn’t figure out to recover from that mistake. So I drew the stools again from scratch, but still hit some roadblocks. I hired another tutor who purported to know both sides of the program and we started from scratch over two hours of lessons. It turns out what he thought was impossible was possible and sent us down a path that was never going to work.
So I drew them from scratch again and started figuring out the rest by myself, which resulted in the first prototype:


I wasn’t happy with the footrest and tried a couple of different revisions, including this terrible idea:

And I finally settled on this template:










The work isn’t finished yet, but I understand that tomorrow is the deadline for the challenge. The final pieces are being cut right now:

After the CNC is finished, I have to:
- Add nice corners to all the edges.
- Prime and paint the FOM logo colors onto the legs and footrest.
- Add and upholster a 1″ red vinyl cushion on the seat.
- Add the hardware to keep the footrest in place when in use and flat pack when in transport
- Figure out the best way to apply the fire effect at the bottom of the stools.
- Sew a simple carrying bag for transport.
Here are the final pieces just before I cut the tabs holding them in the plywood.

The stools are primed and ready for paint


The first round of paint is complete and ready for round 2.


It took a looong time to paint them because it was a huge pain in the ass and I will never do any kind of complicated painting like this again. I was also under a time constraint because I committed to sell one of the stools at an auction, so I eventually had to focus on just one of them, which turned out like these pictures:







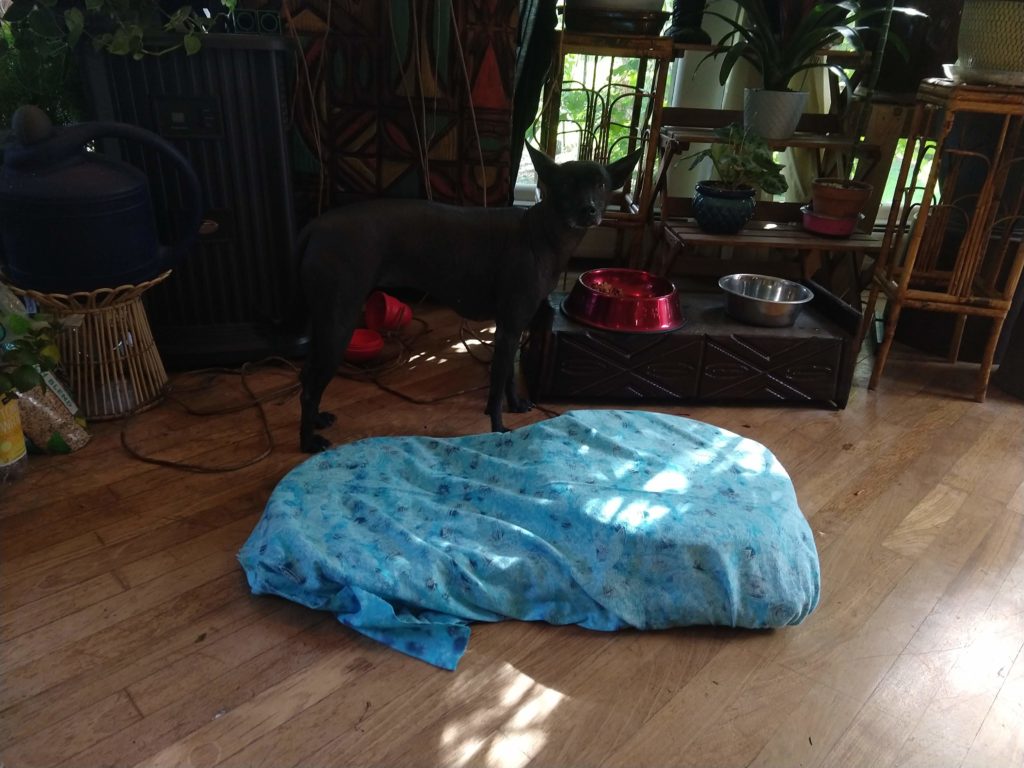
I also had to sew some storage bags, which were basically french seam pillowcases. The auction was a success and it raised over $200 for charity. But, the painting process was such a pain in the ass, I lost motivation and put them on the backburner for another 6+ months and finally knocked the rest of them out.












I decided to sell another one at auction, which we had to carry on the plane, so I made the following carrying case with a plea to the TSA not to mess with it. Southwest charged me for the extra size, but the gate agent told me to contact customer support and tell them it was for charity. That turned out to be a great idea because Southwest reversed the charges before we landed. The carrying case was a success and the stool made it intact and un-marred. The second stool sold for around 139$.

I put the project on hold again for a while and finally finished the remaining stool covers. One now sits in the Tiki room and the other two are in storage waiting for the portable bar to be built.

I am sooo glad this project is over. Now we just have to wait for Lina to paint her stool.
You must be logged in to post a comment.